A six-sigma process is faster more efficient more economical and delivers quality satisfactorily. Population A statistical term used to describe the whole range of possibilities from which a measurement could be taken.
Benefits Of Six Sigma For You And Your Organization
Six Sigma 6σ is a set of techniques and tools for process improvement.
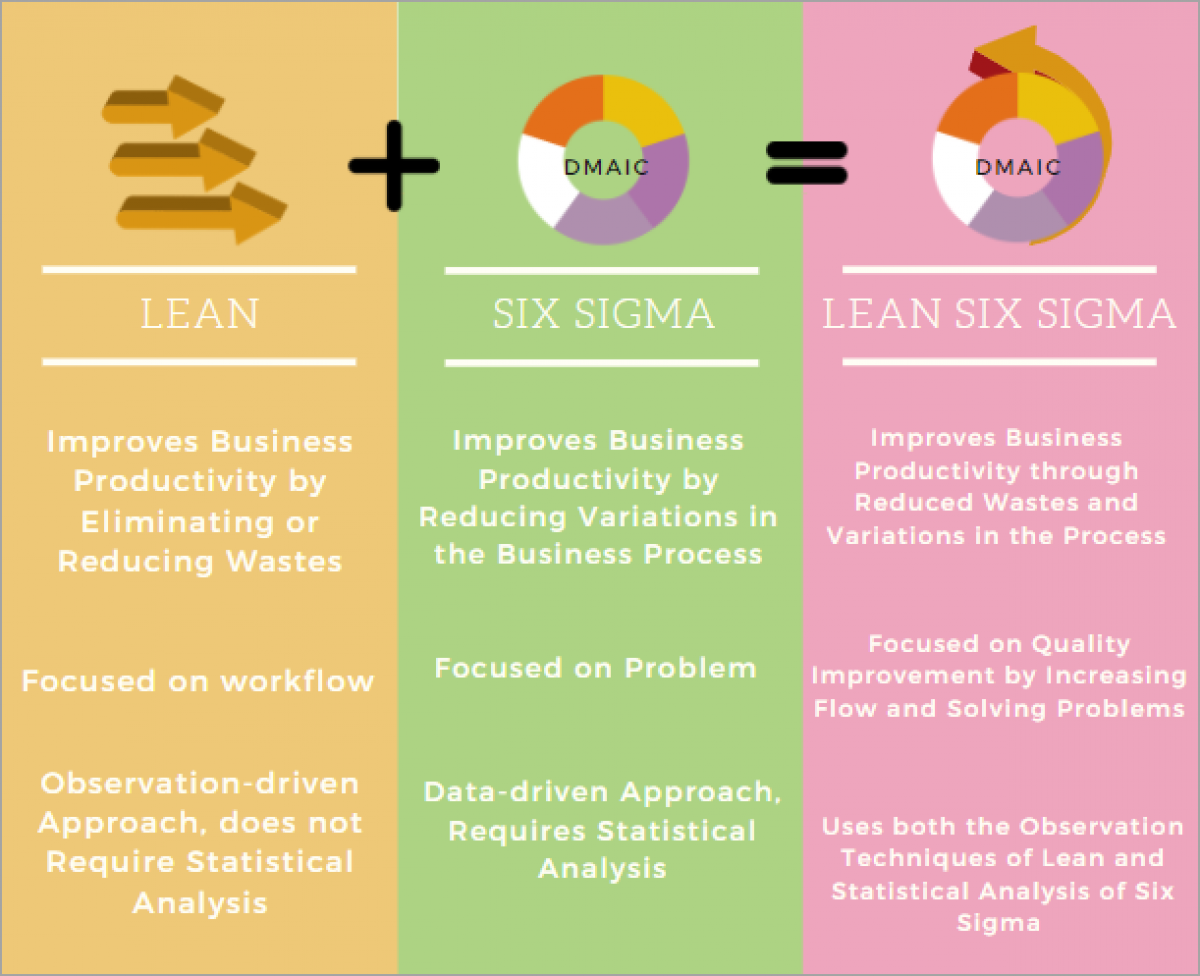
. A Professionals who earn Six Sigma certification become key. Hence a business must understand the needs of their customers. In 1984 a Motorola engineer named Bill Smith developed the Six Sigma management system to reduce the variations in.
Something that is within -6s Six Sigma from the centerline of a control chart was created by a process that is considered well controlled. It was introduced by American engineer Bill Smith while working at Motorola in 1986. Six Sigma strategies seek to.
The main objective is to maximize the benefits for customers. Types of Customers Customers play a significant role in any business. The term Lean was first used to describe the Toyota Business System in the 1980s a business philosophy that helped the company run at maximum efficiency.
Standard Deviation also known as Sigma or σ determines the spread around this meancentral tendency. There are five main principles of Six Sigma. Measures such as Cp and Cpk are used to describe the performance of your process against your specifications whether they be internal or customer-focused.
If the process has six Sigmas three above and three below the mean the. A Professionals who earn Six Sigma certification become key. A sigma quality level serves as an indicator of how often defects are likely to occur in processes parts or products.
It was developed by a scientist in the. The Six Sigma and Lean Six Sigma approaches aim to achieve the same thing. The theory was first introduced by Walter Shewhart in the 1920s.
The Six Sigma Methodology offers a high level of quality that makes every effort to reach perfection in products or services sold by a company organization or business. Present Value Value at the beginning of a time. This method will describe quantitatively how processes are performing.
It is an approach that is data driven and very disciplined for the purpose of getting rid of defects. The fundamental objective of the Six Sigma methodology is the implementation of a measurement-based strategy that focuses on process improvement and variation reduction through the application of Six Sigma improvement projectsThis is accomplished through the use of two Six Sigma sub-methodologies. The etymology is based on the Greek symbol sigma or σ a statistical term for measuring process deviation from the process mean or target.
In other words there is little deviation from the standard and is within tolerance. By better understanding the different types of customers businesses can be better. This is the reason why a 6σ Six Sigma.
A six sigma process is one in which 9999966 of all opportunities to produce some feature of a part are statistically expected to be free of defects. The term Six Sigma came from the statistical modeling of manufacturing processes and sigma ratings are used to describe the maturity of a manufacturing process. Six Sigma is used in the calculations of process capability.
Six Sigma is a term used to describe process improvement initiatives using sigma-based process measures andor striving for Six Sigma level performance. The term Six Sigma refers to a set of quality-control tools that businesses can use to eliminate defects and improve processes to help boost their profits. Six Sigma Terms Definitions - This is a comprehensive listing of common six sigma and lean six sigma terms and their definitions in alphabetical order.
A sigma is a measure of standard deviation abbreviated as small s or the Greek letter σ. Several decades later in 1980 Motorola engineers Chairman Bob Galvin and Bill Smith developed a new measurement. Six Sigma is a term used to describe process improvement initiatives using sigma-based process measures andor striving for Six Sigma level performance.
More effective processes that yield a bigger bottom line. Six Sigma is a data-driven methodology that provides tools and techniques to define and evaluate each step of a process. It involves every tier of an organization helping.
If Six Sigma is your goal improving your process capability will require an understanding of the statistics that are involved. Six Sigma is a methodology used for detecting variation in a process and thus seeks continuous improvement. The more number of standard deviations between process average and acceptable process limits fits the less likely that the process performs beyond the acceptable process limits and it causes a defect.
The goal is to use continuous process improvement and refine processes until they produce stable and predictable results. The processes are executed by Six Sigma Green Belts and Six Sigma Black Belts and overseen by Six Sigma Master Black Belts. It helps to improve products or services by discovering.
Six Sigma is an approach to data-driven management that seeks to improve quality by measuring how many defects there are in a process and systematically eliminating them until there are as close to zero defects as possible. Six Sigma comes from the bell curve used in statistics where one Sigma symbolizes a single standard deviation from the mean. The term sigma is a Greek alphabet letter σ used to describe variability.
A Six Sigma quality level equates to approximately 34 defects per million opportunities representing high quality and minimal process variability. DMAIC is the acronym for Define Measure Analyze Improve and Control the five key phases of the Lean Six Sigma framework used in solving business and process problems. DMADV is the acronym for Define Measure Analyze Design and Verify the Lean Six Sigma method for designing new processes and products.
The Six Sigma DMAIC process. The processes are executed by Six Sigma Green Belts and Six Sigma Black Belts and overseen by Six Sigma Master Black Belts. It provides methods to improve efficiencies in a business structure improve the quality of the process.
Variation can be divided as common cause variation and special cause variation.
Six Sigma Overview Principles And Methodology
Using Six Sigma For Successful Project Management Infinity
Lean Vs Six Sigma Understanding The Lean Six Sigma Methodology
0 Comments